ディップコート法は、製造工程における表面処理技術として広く用いられています。
簡便な操作性と均一なコーティングを実現できることから、様々な分野で活用されていますが、その原理や膜厚制御、適用事例など、理解を深めるには専門的な知識が必要となる場合があります。
今回は、ディップコート法の基本原理から具体的な応用例、メリット・デメリットまでを分かりやすく解説します。
ディップコート法の基本と原理
ディップコートとは何か
ディップコート法とは、ワーク(被処理物)を液体中に浸漬し、引き上げることで表面に均一なコート膜を形成するコーティング技術です。
この方法は、液体の表面張力と重力、そして引き上げ速度を巧みに利用して、ワーク表面に付着する液体の量を制御し、膜厚を調整します。
簡便な操作性と、比較的均一な膜厚を得られることが大きな利点です。
ディップコート法の仕組みと工程
ディップコート法の工程は、大きく分けて浸漬、引き上げ、乾燥・硬化の3つのステップから構成されます。
まず、ワークをコート液に垂直に浸漬します。
一定時間浸漬後、ワークをゆっくりと引き上げます。
この引き上げ速度が膜厚に大きく影響します。
引き上げ後、乾燥や焼成などの後処理工程を経て、コート膜を硬化させます。
後処理工程は、使用するコート剤の種類や求められる膜質によって異なります。
膜厚制御のポイントと注意点
膜厚の制御は、ディップコート法における重要な要素です。
膜厚は、コート液の粘度、密度、そして引き上げ速度の3つのパラメータによって決定されます。
粘度や密度が高いほど、また引き上げ速度が速いほど、厚い膜が形成されます。
しかし、これらのパラメータを調整する際には、コート液の特性やワークの形状などを考慮する必要があります。
膜厚が不均一になったり、ピンホールが発生するなどの問題が起こる可能性もあるため、最適なパラメータを見つけることが重要です。
ディップコート法のメリットとデメリット
ディップコート法のメリットは、簡便な操作性、高い生産性、両面同時コーティングが可能であること、そして様々な形状のワークに対応できることです。
一方、デメリットとしては、膜厚の制御に高度な技術が必要となる場合があること、最初に液槽に入れる大量のコート液が必要であることなどが挙げられます。
また、コート液の選択や後処理工程も、膜質に大きく影響するため、注意が必要です。
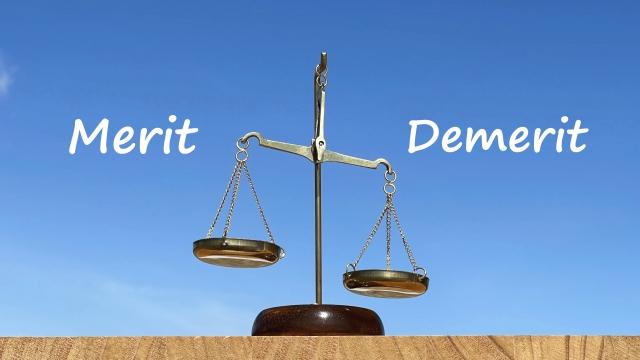
ディップコート法の適用事例と将来展望
様々な分野での活用事例
ディップコート法は、電子部品、光学部品、医療機器など、幅広い分野で活用されています。
例えば、電子部品では、基板への保護膜形成やはんだ濡れ性の改善などに用いられています。
光学部品では、レンズやプリズムへの反射防止膜の形成などに用いられています。
また、医療機器では、生体適合性の高いコーティングを施すために用いられています。
ディップコート法の今後の可能性と課題
ディップコート法は、今後ますます高度化・多様化していくことが予想されます。
ナノレベルでの膜厚制御技術や、新たなコート液の開発などが進められています。
しかし、環境負荷の低減やコスト削減といった課題も残されています。
関連技術との比較
ディップコート法と比較されるコーティング技術としては、スプレーコーティング、スピンコーティングなどがあります。
それぞれの技術には、適用できるワークの種類や膜厚の均一性、生産性などに違いがあります。
どの技術が最適かは、ワークの形状、材料、求められる膜質などによって異なります。
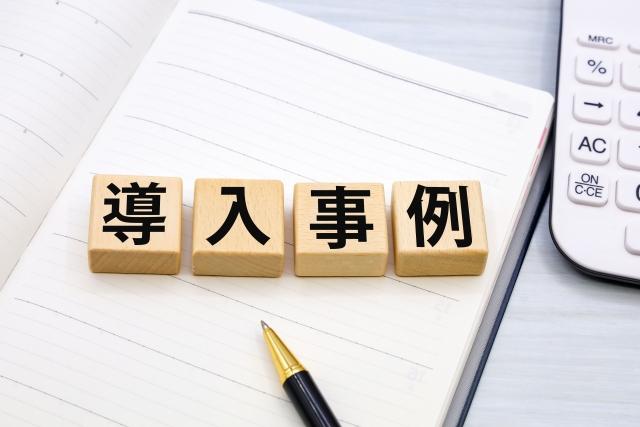
まとめ
今回は、ディップコート法の基本原理から、具体的な適用事例、メリット・デメリット、そして将来展望までを解説しました。
ディップコート法は、簡便な操作性と均一なコーティングを実現できることから、様々な分野で活用されていますが、膜厚制御やコート液の選択など、高度な技術が求められる側面もあります。
本記事が、ディップコート法の理解を深める一助となれば幸いです。